Intro
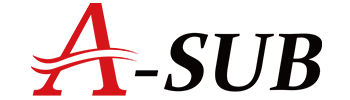
As a leading manufacturer of inkjet photo papers, our factory is committed to pursuing environmentally sustainable production practices. However, as a mid-sized facility, our options for large-scale initiatives are sometimes limited by operational and financial constraints. While we aspire to world-class standards of eco-efficiency, our immediate priority must be continuous enhancement through pragmatic, low-cost solutions.
Improving Energy Efficiency
●Optimizing Production Processes to Reduce Energy Loss
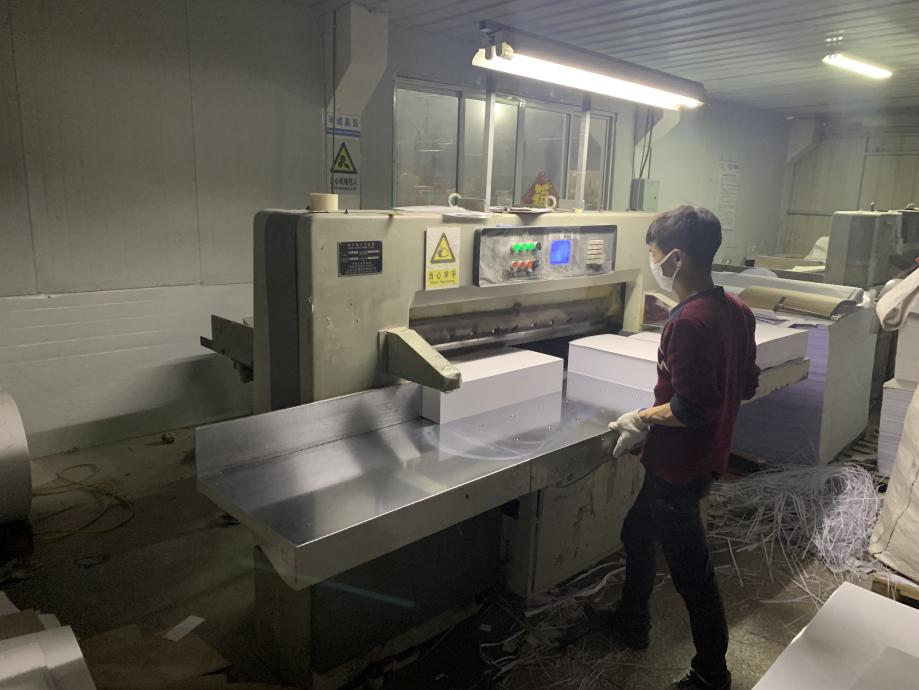
Our factory is undertaking a thorough review of all process steps with an eye towards trimming wasted energy. One focus is the moisturizing stations, which currently operate continuously despite intermittent paper stock. By installing proximity sensors activating the mists only when required, we estimate saving 120,000 kWh annually.
Another evaluation targets periods where paper awaits the next stage too long in temperature-controlled spaces. Optimizing internal material flows through mapping and digital tracking aims to reduce such idle times by 25%. Combined with lowering thermostat setpoints 2-3°C when possible, modeling suggests slashing related conditioning costs by 5%.
●Upgrading High-energy Consuming Equipment
As part of scheduled cyclical investments, we are prioritizing energy-inefficient machines near the end of their working lives. One such item is a aging water chiller for solvent recycling requiring urgent replacement. A variable speed unit sized precisely for needs would use 30% less power annually than the outdated model.
Meanwhile, fluorescent shop-floor lighting reaches the maintenance threshold after 15 years in service. Transitioning to LED panels trimmed overall consumption by 20% when tested in receiving areas. With a 2-year payback estimated, this initiative rolls out economy-wide in phases to maximize savings.
●Promoting Energy-saving Work Practices
Employee engagement campaigns stress wise behaviors like minimizing open sacks or canopies when powdered materials stand undisturbed. Work schedules now cluster heating processes and equipment cleaning to off-peak utility rates times. When combined with targeted reminders and team competitions, these efforts helped curb demand by an auspicious 4.5% last quarter. As awareness builds, we project the savings rate can be sustained and surpassed going forward.
Constant improvement is key to conserving finite resources responsibly. By optimizing, upgrading and promoting best practices, our factory strives to curb energy use intently each year.
Water Resource Management
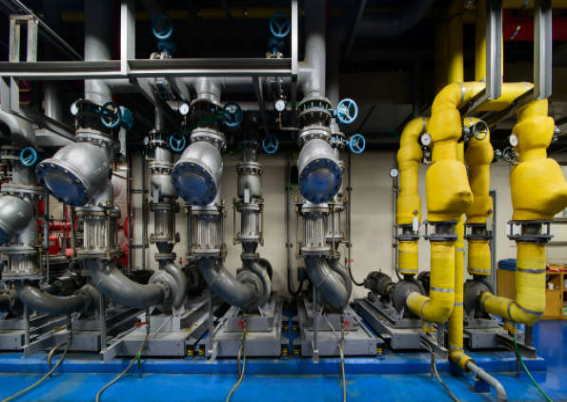
●Recovering and Reusing Water in Production Processes
Our factory captures water from various production steps to reuse wherever possible. Drainage from paper conditioning and washing is directed to settling tanks for particles to deposit. Clarified liquid then undergoes microfiltration and ultraviolet treatment before blending into dispersions requiring lower purity. This closed-loop system currently reroutes over 60% of waste streams internally.
We also harvest rainwater from plant rooftops through gutters into cisterns. Processed similarly, this "grey water" boosts total recovery volumes while recharging the aquifer less than municipal sources. Metrics show substituting 10% of annual intake has already been achieved, exceeding initial five-year targets.
●Lowering Temperature Differences to Increase Efficiency of Recycling Systems
Water recycling plant temperature is finely tuned to within one degree of process needs to minimize heating costs. Piped return streams from manufacturing preheat incoming makeup flows using a series of plate heat exchangers. Temperature sensors provide real-time readings to continuously adjust boiler outputs downwards without compromising quality.
Heat recovery from boiler flue gases also helps preheat air in winter, offsetting space heating demands. Insulating distribution pipes further reduces losses delivering tepid water for landscaping rather than wasteful dumping.
●Reducing wastewater generation
We diligently reduce wastewater volumes requiring external treatment by redesigning rinse stages. Migration from continuous flowing to countercurrent rinse cards sharply curbed rinse water use. Recovery totes now concentrate lower-strength waste for later reuse, keeping strongerstreams isolated for on-site treatment before legal discharge.
Conserving Raw Materials
●Rational Use of Materials to Avoid Waste
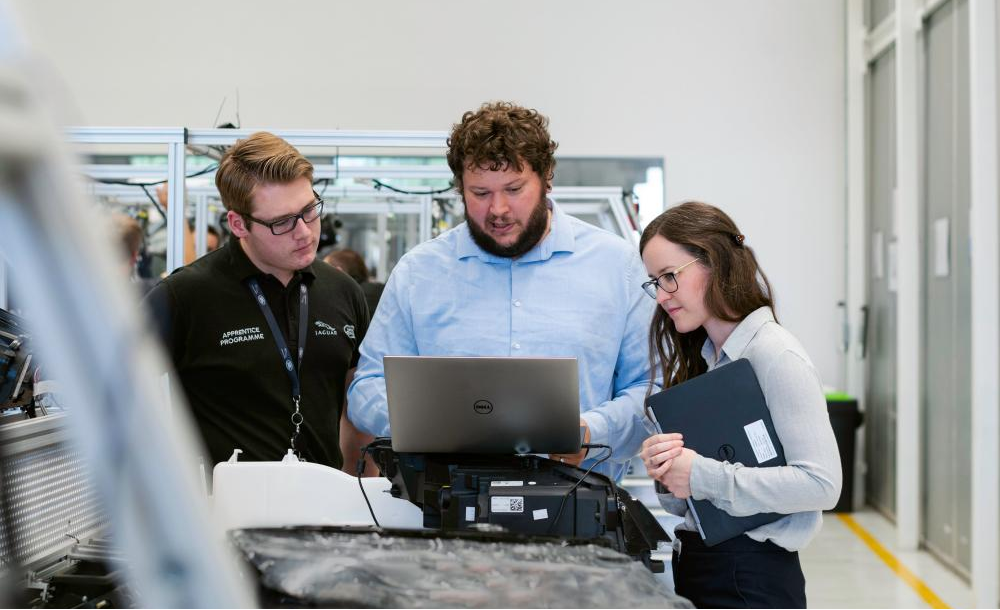
To eliminate waste of valuable paper pulp and chemical resins, our operators undergo training emphasizing careful handling. Digital scales in production areas objectively track usage per batch for anomalies. Adjustments minimize over-dispensing through precise metering nozzles on tanks.
Work-in progress inventory is tightly controlled to avoid material expiration before conversion. First-in, first-out protocols expedite older stocks while still viable. Where minor defects once meant waste, repair strategies now salvage reworkable paper trim for lower grades.
●Promoting Digitalization to Reduce Sample Production
Adopting computer-aided manufacturing software slashes physical sample-making. Customers collaborate online to visualize specs, tweak formulations and approve designs virtually before market trials. Digital “proofs” require no paper or chemistry use compared to physical samples’ material demands. Since launch, digital prototyping has slashed sample production by 15%.
●Recycling Internally Generated by-products
All reusable production residues undergo sorting for reintroduction. Paper fiber from trimming and edgeleting machines reground into pulp for non-critical base paper grades. Reclaimed coating pigments receive attrition milling for reuse rather than landfilling. Solvents from washing undergo distillation to recover ultrahigh purity solvents for another cycle. Together, these initiatives divert over 95% of waste from external disposition.
Going forward, even greater circularity will optimize material efficiency through innovation. But consistent focus on conserving valuable inputs through rational practices, digitization and inner-loop recycling presently enhances sustainability.
Controlling Emissions
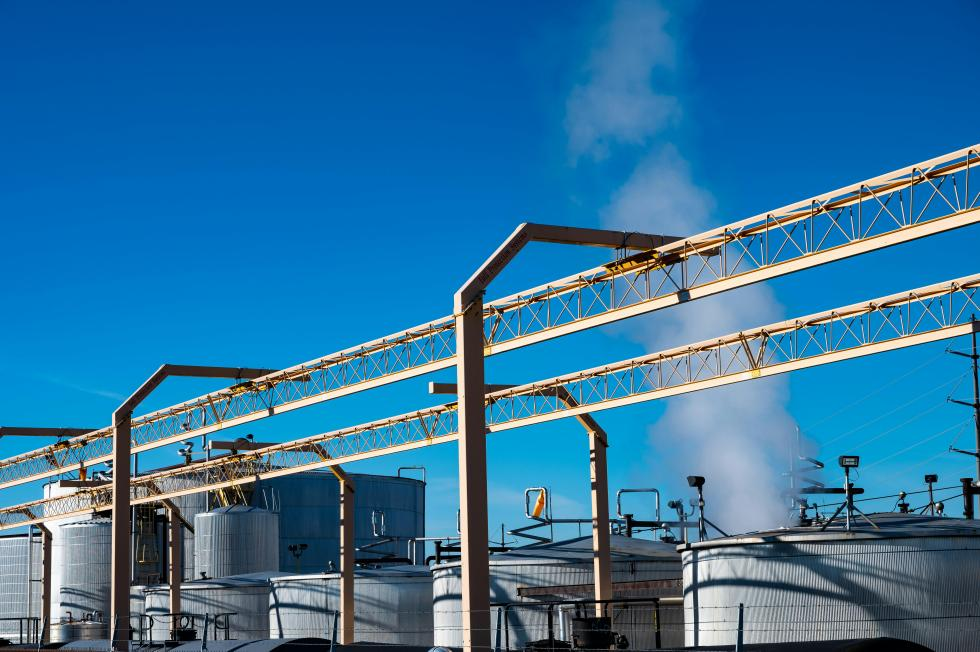
●Regular Maintenance of Emission Treatment Equipment
Strict preventative maintenance is performed on air pollution control devices like boilers, dryers and recovery ovens to ensure peak performance. Fume hoods and ductwork undergo thorough washdowns every shutdown to remove accumulated particulates. Filters and scrubbers are replaced ahead of the design life cycle to guard against degradation.
Comprehensive logs track all inspection, testing, repair and calibration activities to demonstrate regulatory compliance. Proactive repairs also minimize unexpected downtime and costs from exceeding emission limits.
●Strengthening Monitoring of Vehicle Exhausts
Idling reduction and routing policies shed unnecessary trips to shave greenhouse gas emissions. A fleet management system closely monitors engine run-time and driver behavior via telematics. Those exhibiting poor fuel efficiency receive evaluation and retraining where needed.
All forklifts transitioned to lithium-ion power to eliminate emissions in the plant. And ten percent of ground transport will be electric by 2025.
●Adopting Low-cost Measures to Minimize Environmental Impact
Simple adjustments like optimizing boiler airflow ratios lowered nitric oxide creation by 15%. Fine-tuning dryer flame characteristics minimally yet appreciably reduced carbon in flue gases.
New coatings on powder collection bags prolong service life twofold while shedding a micron of particles previously emitted on change-out. Lifting the plant speed limit discourages habits wasting fuel. Together, low-hanging solutions steadily shrink our footprint.
Ongoing commitment to modernizing equipment and empowering personnel sustains progress in controlling emissions responsibly year after year.
Waste Management
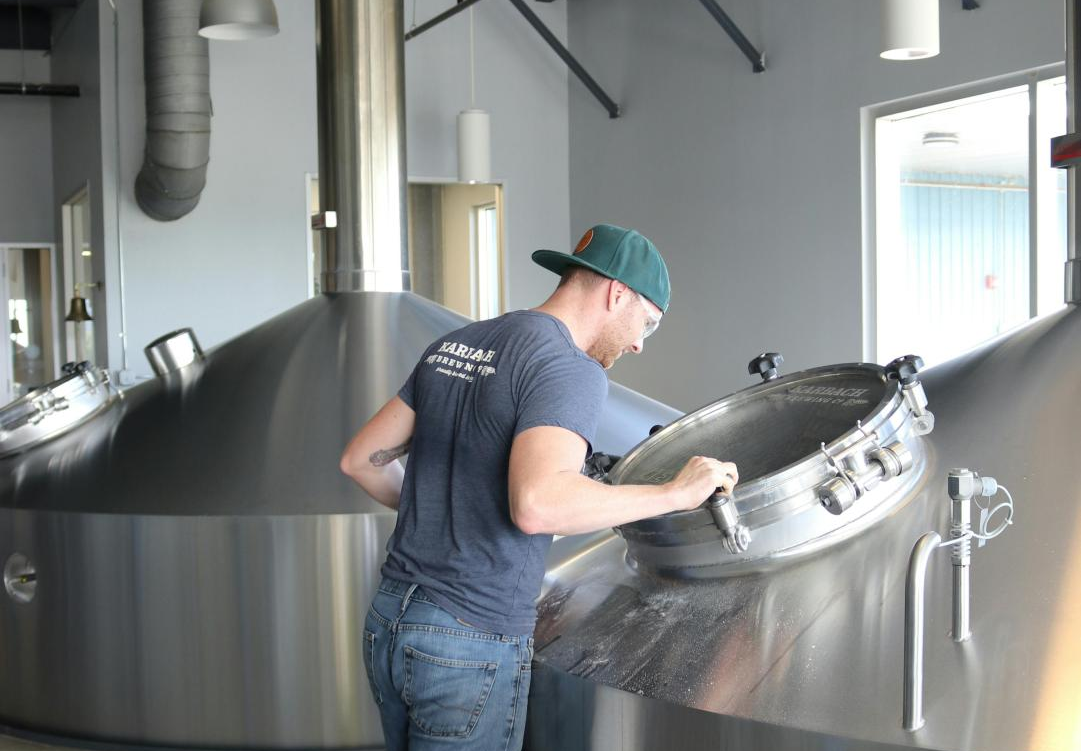
●Proper Handling and Disposal of Hazardous Waste
Weekly hazardous collections enter stringent manifest and transportation procedures. Our plant teams hold emergency response training yearly in tandem with disposal vendors to facilitate rapid, legal spill containment.
●Recycling of Recyclable Materials and By-products
All clean paper trim, overruns and rejects enter baling directly for combustion as renewable fuel. Efforts continue optimizing production to minimize such volumes.
Recoverable plastics like sleeves and spacers undergo shredding and pelletizing for remelting. Metal components from equipment repair scrap dealers for reprocessing.
Even complex residues undergo evaluation. Pigment mud once landfilled now undergoes thermal debinding and smelting to liberate zinc oxide valorized as micronutrient fertilizer.
●Reducing Use of Disposable Items
To curb solid waste, we phased out single-use coffee cups, utensils and lunch containers in favor of employee-washable versions. Trash has minimized through restricted purchases and "packaging amnesty" encouraging reuse of delivery containers.
Going forward, a zero-waste certificate depends on eliminating all disposables while boosting recycling participation. Leveraging reusable and remanufacturable items elevates our progress.
Prioritizing proper waste handling and maximizing recycling closes material loops responsibly. Each success enhances efficiency and environmental performance.
Fostering Environmental Awareness

●Employee Environmental Training
All new hires undergo orientation covering sustainability priorities and their individual role. Targeted job training reinforces procedures around energy, water and materials conservation.
Lunch-and-learn seminars update staff regularly on upcoming initiatives for engagement. Department-specific sessions delve into operational changes and accountability. An eco-newsletter shares monthly progress and best practices plant-wide.
●Establishing an Image as a Green Factory
Signage at our entrance and in main areas emphasizes green accomplishments and goals. Dedicated space on the intranet and notice boards showcase initiatives and employee contributions using success stories and metrics in everyday language.
External marketing highlights sustainable paper qualities benefits and production ethics. Tours for suppliers and the community spread understanding of continual improvements visible facility-wide.
●Soliciting Suggestions for Improvement
An eco-committee representing all shifts gathers regularly to survey operations for new efficiencies. An anonymous green ideas box collects submissions rewarded through quarterly drawings. An annual eco-innovation contest attracts numerous entries evaluated for feasibility and savings potential.
Since launching, over 75 staff recommendations have been implemented -- from simple adjustments like task scheduling to major capital projects. Continued two-way communication sustains momentum for both environmental and morale benefits.
Prioritizing environmental education and participation across the workforce strengthens individual commitment to sustainable practices as a united factory.
Conclusion
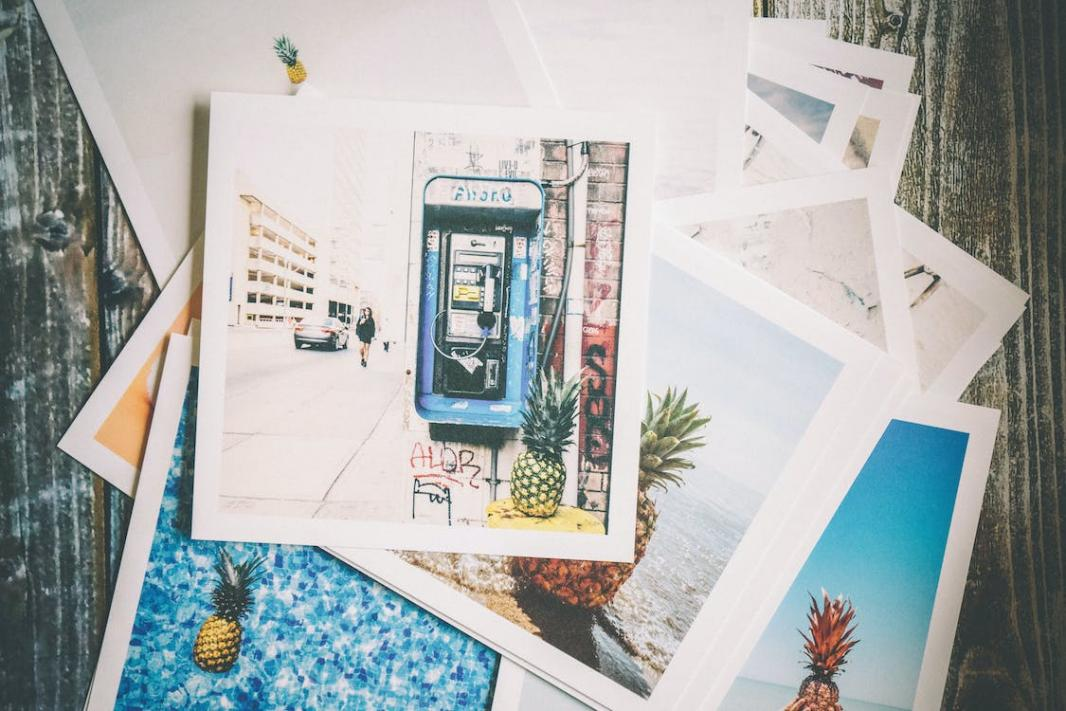
Through diligent focus on continuous improvement, our factory has realized significant gains across multiple fronts of environmental performance in recent years. Routine optimization of production workflows and processes has substantively trimmed energy consumption while water recycling now returns over 60% of usage back into manufacturing.
Careful material stewardship combined with digital prototype solutions has slashed sample production’s raw material demands. Proactive equipment servicing maintains air and water emissions control at full proficiency. Waste diversion initiatives successfully recover 95% of by-products from landfilling by funneling them back internally or through end-of-life recycling.
Employee involvement through education, communication and green idea sharing nurtures a culture that increasingly thinks sustainably in day-to-day duties. Externally, establishing our brand’s environmental credence attracts forward-looking partners helping augment effectiveness.
Most importantly, unrelenting focus on enhancing resource efficiency through constant small measures, just as with manufacture quality, will future-proof our business from volatility. Remaining agile enough to seize opportunities that arise will propel our sustainability trajectory alongside industry peers. Our factory is committed to this prudent, long-term vision empowering community well-being and environmental protection in tandem with responsible commercial success.
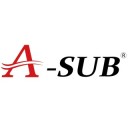